Allion Labs / Ken Yan
長年にわたってお客様の取り組みをサポートしてきた中で、納期や時間のプレッシャーに縛られて、製品検査で合格できないお客様がよくいらっしゃいました。分析すると、多くが製品設計、受け入れ検査、製造初期の各段階で解決しなければならない問題が原因であることが分かりました。このような状況が発生すると、時間の無駄なだけでなく、設計の修正コストも増加するため、各段階で製品の品質パフォーマンスを把握できれば、出荷前のトラブルを大幅に減らすことができます。
不良の原因を分析する前に、まず生産ラインにおける各検査およびコントロールの各段階を理解する必要があります。品質管理プロセスには、基本的に次の様な4つの手順があります。
1. 入荷品質管理
2. 製造プロセスの品質管理
3. 製品検査
4. 出荷検査
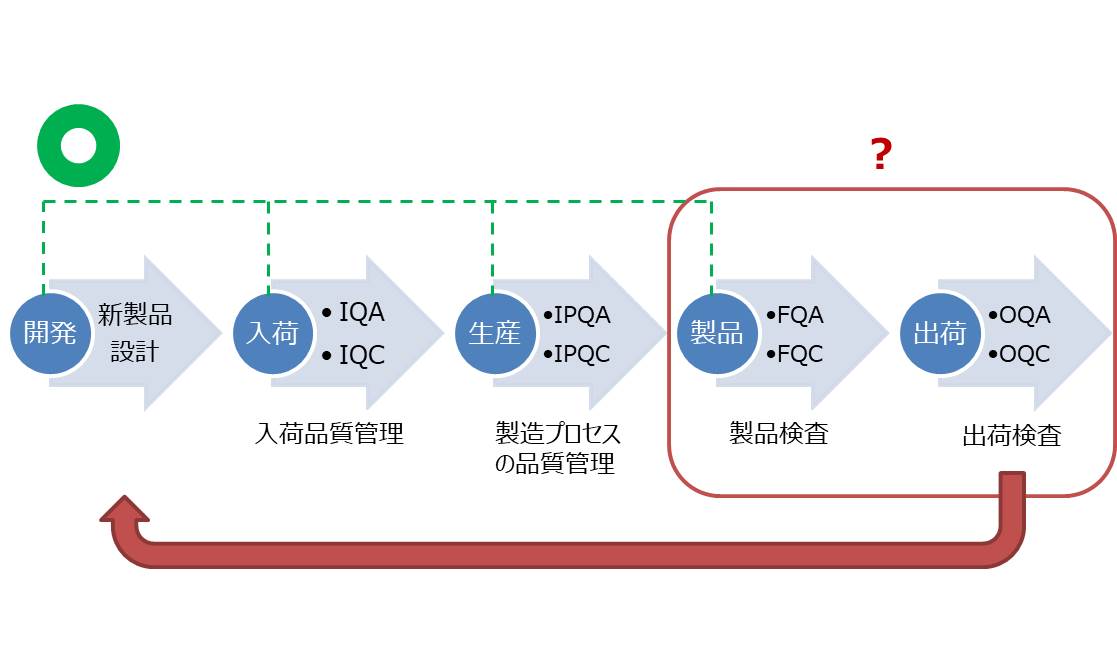
本文の重要なポイントは、同軸ケーブルに関する開発と入荷、そして製造プロセスの管理で注意すべき点です。前段階と中段階における設計や素材の特性や加工コントロールに留意しできれば、出荷時の製品品質を大幅に向上させることができます。
1. 新製品開発の段階
開発の初期段階では、エンジニアが製品の各部品に対して厳格なテストとクロスチェックを行い、自社製造もしくは外部調達でどのような部品を使用するかを決定し、部品の設計、組み立て、相互の互換性を確認する必要があります。よくある注意点には以下が含まれます。
A. 部品の選択
アセンブリ部分では、コネクター、裸線、パドルカードの特性品質や構造の強度に加え、加工エリアで塗布する接着剤の種類も定義しなければなりません。製品設計の早い段階で、接着剤の特性や量産時に加工性、含水量、硬化時間などの各要素に対応できるかなどを考慮する必要があります。
B. 部品特性の損失余裕度
裸線部品の選定に際して、コネクターと加工部分に対して損失マージンに注意する必要があります。USB Type-C Gen2ケーブルを例に挙げると、HostとDeviceの許容損失は8.5dBであり、製品ケーブルは5GHzで6dBです。この場合、選定した裸線特性が5GHzで既に5 dBを超えていれば、コネクターと加工による損失を加えると、スペックをオーバーしてしまう可能性が非常に高くなります。
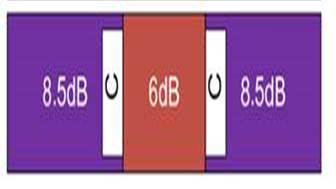
C. パドルカード(Paddle Card)コントロール
PCBレイアウトメーカーが受注後、仕様の基準によるインピーダンスの設定を従ってTraceとPadを設計し、その後線材メーカーがパドルカードを取得し、実際に裸線をはんだ付けして接着したところ、加工後の電気容量により当初設定されていた特性インピーダンスが低下し、逆にインピーダンスの不連続性が増加したことが判明しました(下図を参照)。これは、製造業者とレイアウト業者が発注時に後続の加工やそれに対する影響について話し合っていなかったことを示しています。正しい方法は、加工後に発生する特性インピーダンスの差異を事前に見積もり、レイアウト時に特性インピーダンスの設計を高めて、加工後の波形が適切な範囲内に収まるようにすることです。
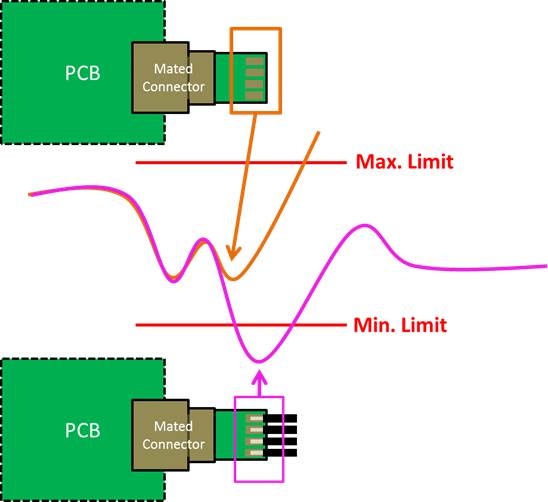
図:Paddle Cardはんだ付け前後の差
D. 生産プロセスについて
- 裸線各層の剥線の長さを明確に定義し、それに基づいて剥線機のパラメータを設定する必要があります。レーザー剥線機を使用する場合は、剥線する材料に応じて、上下の列のエネルギーと焦点も明確に定義する必要があります。
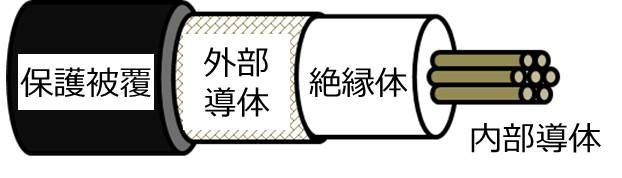
図:同軸ケーブルの構造
- はんだ付けはパドルカードの設計に合わせて機種の選定が必要であり、HotBar(熱圧着はんだ付け)方式を使用する場合は、ヘッドタイプ、適切な温度設定、ストローク設定、押し付け時間などのパラメータを考慮する必要があります。
- 巻き付け式の編み込みやバンディングを選択する場合、従来型の水平式機械は地球の引力の関係で包装の均一性に影響する可能性がありますが、直立式機械は動作方向が地球の引力に垂直であるため、包装の不均一性によるノイズ耐性問題を改善できる可能性があります。
2. 受け入れ検査
すべての部品に対して検査を実施することは非常に重要です。量産時の部品の構造や特性、スペックに合わない場合は、製造前に問題を特定する必要があり、特定できなければ、生産後に時間やコストの損失が発生する可能性があります。特性に関連するよくある問題には、次のものがあります。

A. 裸線
- 線材構造の正確性例(シールド層、グランド線および配線の配置が間違っていると、不良なクロストークを引き起こす可能性があります)
- 特性インピーダンス設計の正確性(例:波形が滑らかで歪みが少ないか)
- 挿入損失のパフォーマンスが想定通りか(例:検査時に減衰量が評価値より大きい場合、エンド製品の線路特性に悪影響を与える可能性があります)
- 共・差動モードの変換損失が高すぎないか(絶縁層の包み込みが均一でない場合や、ケーブルの長さの差が大きすぎる場合も、この不良の原因になる可能性があります)
- 編み込み密度が指定されたパーセンテージに達しているか(例:EMI特性に影響を与えます)
B. コネクタ
- 端子の位置が正しいかどうか(例:端子がずれていると、高周波の特性不良、特にクロストークを起こす可能性があります)
- 端子にバリが生じていないか(バリがあると、損失が大きくなる可能性があります)
- SMTの端子間隔が設計に合っているか(間隔が合わないと、パドルカードとの位置合わせが困難になる可能性があります)
C. パドルカード
- 特性インピーダンスの設計が正しいか(例:はんだ付けの後に特性インピーダンスが低下し、テスト結果に影響を与える可能性があります)
- グラウンドループが正しいか(例:グラウンドループが不良だと、クロストークも悪化する可能性があります)
- 異なる基板層間で信号が変換される際、ベアリングが相互干渉するか(密接すると特性インピーダンスとクロストークに影響を与える可能性があります)
- ボードカットがボードの端の寸法に影響するか(例:サイズが合わないと組み立てが困難になり、高周波特性に影響を与える可能性があります)
3. プロセス品質コントロール
全ての準備が完了して製造プロセスに進む前に、生産における全てのプロセスが事前に計画され、設備が調整されていることを確認する必要があります。様々な設備には、理想的なパラメータと現状との間にわずかな誤差が必ず存在するため、設備のパラメータと設定が合わない場合、エンド製品の特性が期待に沿わない場合もあります。以下によくある状況を示します。
- 切断時、切断刃が鋭利かどうか
- SMTやコネクタの配置がずれていないか
- はんだ付け時の温度が高すぎて芯線が収縮して変形していないか
- はんだ付けの時に芯線が分岐したり、緩んでいないか
- はんだ付けの時にスズボール(線)、空はんだ、ショートなどの現象が生じていないか
- 同軸ケーブルの編組が完全に被覆されているか
- 内部ゴムが特性インピーダンスに過度に影響していないか
- 内部ゴムが十分に乾燥・固化されているか
事例共有
上記の説明を踏まえた上で、実際のテストで遭遇した一般的な不良事例を何件か皆様に共有します。以下の例では、該当プロジェクトの不具合問題とその原因の判断を簡単に説明し、最適化後のデータ改善度を示します。
ケース1
<アリオンが提案した改善案>
1. はんだ付け加工の際に加熱時間に注意し、加熱時間が長すぎて線芯の外側が収縮・損傷しないようにしましょう。
2. 加工時には、アルミ箔の長さを余分に剥がさないように注意しましょう。アルミ箔は特性の偏差を防止し、インピーダンスの制御に役立ちます。
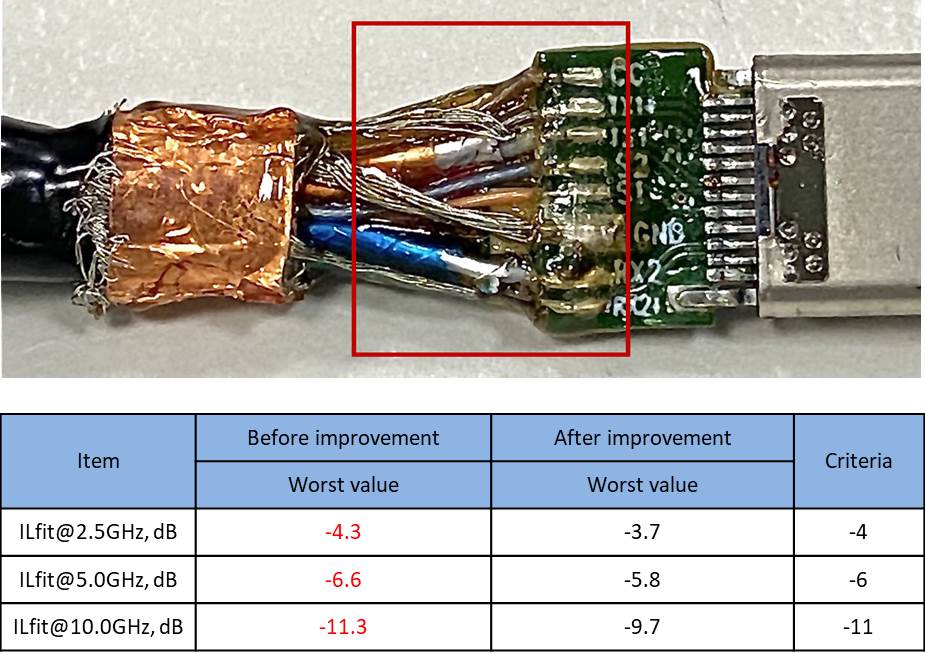
ケース2
<アリオンが提案した改善案>
はんだ付けを実施するポイントのはんだ量と間隔をコントロールし、距離が近すぎてクロストーク現象が発生しないようにしましょう。
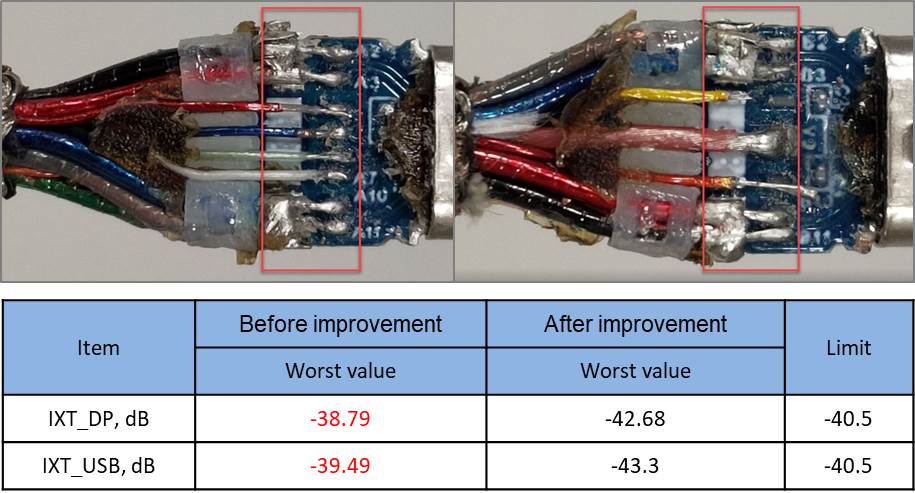
ケース3
<アリオンが提案した改善案>
部品や加工段階でのインピーダンスの不連続性が多大過ぎると、IL Fit、IMR、IRLなどの項目に悪影響を与え、不良が発生する可能性があります。
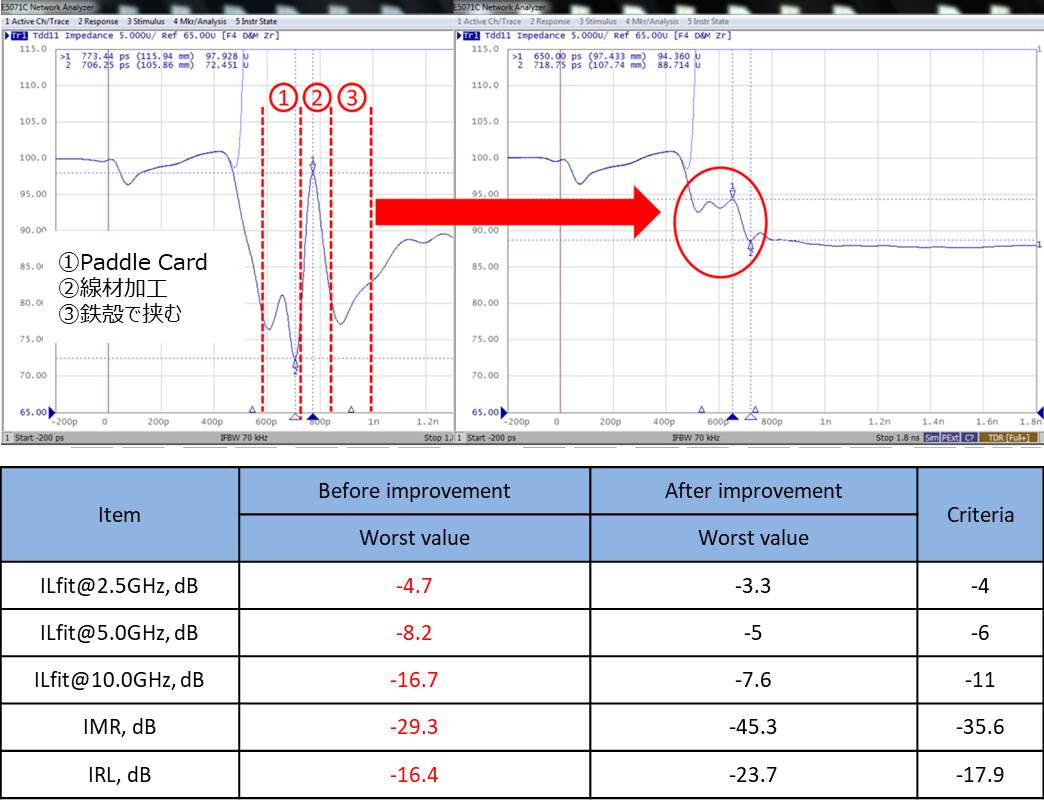
アリオンが提供できる検証サービス
高周波の測定不良の原因には、多くの可能性があります。同じ項目でも、異なる単一/複合要因によって起こるのかもしれません。アリオンは、テストプロジェクトに臨む際、常に最も厳格な態度と迅速な対応方法を持ち、サンプルの設計方法とテスト波形の比較で、最良な改善案をお客様に提供しています。開発初期や認証時に直面する問題にも、より迅速なソリューションを提供することができます。
関連の検証テストサービスについてより詳しい情報をお求めの場合は、アリオンのお問い合わせフォームよりお気軽にご連絡ください。