前回の記事では、IPQC検査の方法と標準的な手順の概要を説明しました。続いて、IPQCにおけるアリオンのQCサービスを詳しく紹介します。アリオンには、製品品質、数量、パッケージ、外観等全てが顧客の要件を満たし、製品品質の管理を効果的に改善するための一連の緻密な検査仕様と計画があり、製造開始から出荷までの製品品質を管理し、品質の信頼性を向上させることをお手伝いいたします。
アリオンによるサービスの特徴
ソリューションの提供と評価
検査プロセスと結果に対する即時フィードバック分析と提案評価、および検査プロセスの明確な記録を進め、プロセスの見落としを徹底的に調査し、実行可能なソリューションを提供します。
包括的な検査と計画
包括的な検査を通じて、検査プロセスにおける死角の最適化と検査計画の改善を実施。また、検査終了後、最初と最後のロットを検査し品質管理を行います。
品質データベースのデータ化
過去の検査内容を定量的に分析し、生産時とローンチ後に発見された問題を同時に更新・記録することで、予防策やアドバイスをリアルタイムで提供します。
品質管理のシステム化
過去のIPQCプロセスデータを記録し、顧客へのフィードバックと提案を週次/月次レポートの形式で提供し、エンドカスタマーからの苦情の割合を記録することにより、定期的且つ定量的でシステマチックに製品を管理します。
以下、実際にあった4つの事例を元に、アリオンが提供するサービスについてさらに深堀りしましょう。
事例紹介1:製品説明書にページ番号がない
Sampling Rate/ Fail Rate
ランダム検査の過程で、1冊の説明書にページ番号がないことが分かり、すぐに100%の製品検査が行ったところ、すべての説明書にページ番号がなく、問題発生の確率が100%であることが判明しました。
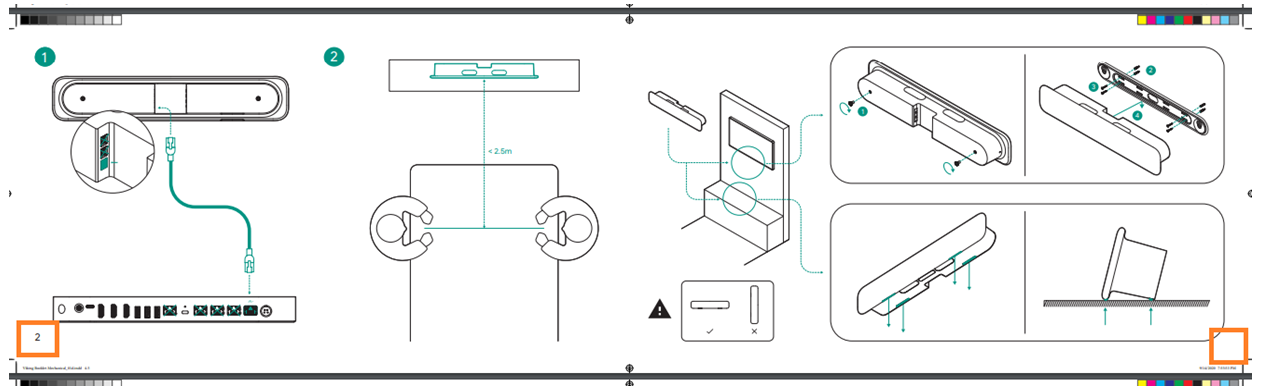
Value
1. 既存の生産ラインプロセスの作業手順(SOP)では、この欠陥を検出することは困難だったため、工場がSOPを更新し重点的に検査することをサポートし、欠陥製品の流出を回避しました。
2. プロセスにおける見落としや標準ではない操作方法の特定をサポートし、製品の不良率を大幅に減少させ、不良品流出によるクレームをゼロにしました。
Root Cause
1. 生産ラインのSOPにはページ番号を確認する項目がなく、検査員はこの欠陥を検出できませんでした。
2. サプライヤーが提供する説明書用の紙に設計上の欠陥がありました。
Solution
1. OQC時に不良の図を総合検査SOPの中に加え、重点的に検査します。
2. サプライヤーが提供する説明書用の紙を改めて設計し直し、不足しているページ番号を追加します。
事例紹介2: Mesh PSA(Pressure Sensitive Adhesive) 感圧ゴムパッドの不良
Sampling Rate/ Fail Rate
ランダム検査の結果、2つのメッシュPSAが部分的に欠落していることが判明しました。すぐに100%の製品検査が行ったところ、このロットの400ユニットのうち30個に欠陥があり、問題発生率は7.5%にまで達していました。
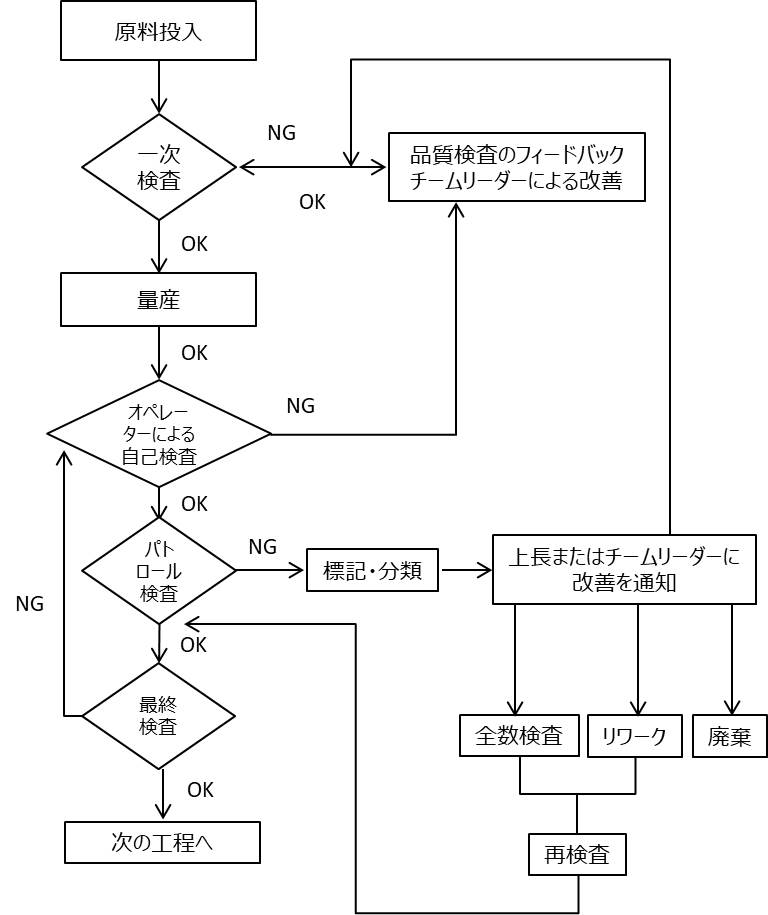
Value
1. 不良品の流出を防ぐために、工場がSOPを更新し重点的に検査するのをサポートしました。
2. プロセスにおける見落としや標準ではない操作方法の特定をサポートし、製品の不良率を大幅に減少させ、不良品流出によるクレームをゼロにしました。
Root Cause
1. 原材料の不良がありました。
2. IQCランダム検査の頻度が不足しており、この欠陥を検出できませんでした。
Solution
1. 受入検査を強化し、次のプロセスへの流入を防ぎます。
2. 工場内の在庫をフィルタリングします。
事例紹介3: 電源供給設備の不良により、システムが起動しないという比較的深刻な問題に
Sampling Rate/ Fail Rate
ランダム検査の過程で、1つの電源装置に欠陥が見つかりました。すぐに100%の製品検査が行ったところ、このロットの182ユニットに欠陥は見つからず、問題の発生率は0.55%でした。
Value
不良率は低いものの問題が比較的深刻であり、既存の生産ラインプロセスの作業手順では、この不良を効果的に検出することは困難であったため、不良品の流出を防ぐために、工場がSOPを更新し重点的に検査することをサポートしました。
Root Cause
電気の物理的損傷(EPID, Electrically induced physical damage)
*指定されたスペックの限界値を超える電流または電圧下における電子機器への熱損傷
Solution
1. 電源供給設備の欠陥有無を相互検証して確認し、メーカーの品質担当とダブルチェックします。
2. 工場内の在庫をフィルタリングします。
事例紹介4:イヤホンジャックのテスト不良
Sampling Rate/ Fail Rate
ランダム検査の過程で、1つのイヤホンジャックのテスト不良が判明し、このロットの問題の発生率は0.09%でした。
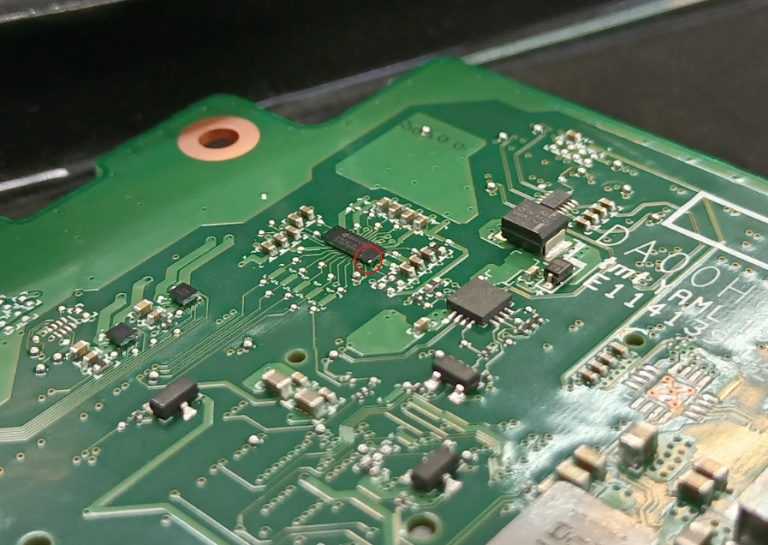
Value
1. 不良品の流出を防ぐために、工場がSOPを更新し重点的に検査することをサポートしました。
2. プロセスにおける見落としや標準ではない操作方法の特定をサポートし、製品の不良率を大幅に減少させ、不良品流出によるクレームをゼロにしました。
Root Cause
MB部品に衝突痕があり、組み立て中に作業者がMB部品を破損した疑いありました。
Solution
1. 生産ラインオペレーターのトレーニングを強化し、同様の不良品の流出を防ぎます。
2. SOPの項目を重点的に検査し、同様の不良品の流出を防ぎます。
実際に起こった上記4つの事例は、アリオンが提供するサービスの簡単な記述と説明の一部に過ぎません。4つの主要なサービスの利点、即ち、ソリューションの提供と評価、包括的な検査と計画、データベースのデジタル化、品質管理のシステム化で、お客様の製品品質の向上をサポートいたします。
この他にも、アリオンは多くの検証サービスを提供しており、ご希望の設計要件や通信品質を通じて、お客様が最短期間で製品品質をチェックできるよう対応することができます。何かご要望がございましたら、お問い合わせフォームよりお気軽にご連絡ください。