この前にご紹介した文章(工場の製造工程における入荷品質管理(IQC)の重要性:概要編、事例編)を読むにあたっていくつかの固有名詞をについて理解を含めた後、実際に工場で出た問題とこれまでの経験の中で見つかった原因と解決方法について見てみましょう。アリオンがSMTの生産ライン上にてどのようにユーザーの方々のコストや時間を節約させているのかを理解することで製品の競争力をさらに高めることでしょう。
事例紹介
事例1. チップピンの接続不良
Spec:
VP6116RYM HF (DC:2145)基盤上に半田付けの不良が見つかり、それによって接続されなくなるケースです。ピンの足に不備があった確率は4/605=6611DPPM (defective parts per million)と言われています。
Action Item:
現場の確認ではピンの足が錫とは接触しているが溶接されてはおらず、ピン自体の軽い反りも確認されたため1ピース全てが接続不良になってしまったケースです。
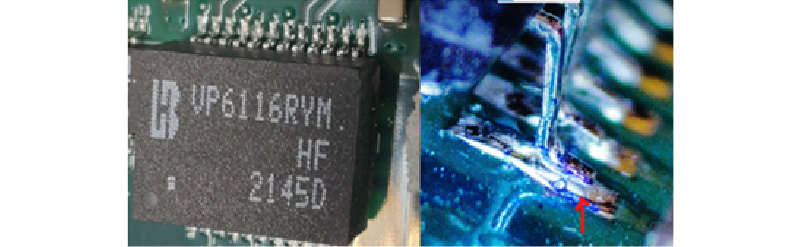
Value:
なぜこのような不良品が産まれてしまうのかサンプルを用いて分析を行いました。まず製品を取り外しましたがピンの足に錫の粘り気があるため、溶解炉でピンにメッキをかけたのち40倍の分光分析装置を用いて平坦度を測定しピンの足がわずかに反っていたものはちょうど0.1 mm目盛を指しました。
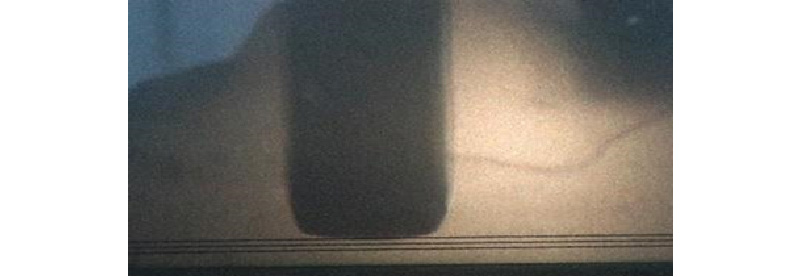
Root Cause:
- Step 1. 投影機ステーション
a. 投影機を使用し状況を確認:40倍の分光分析装置で平坦度を測ります。その時の平坦度の基準は0.1 mm以下とし、さらには0.08 mm以下(図3のように)まで厳しく判断します。
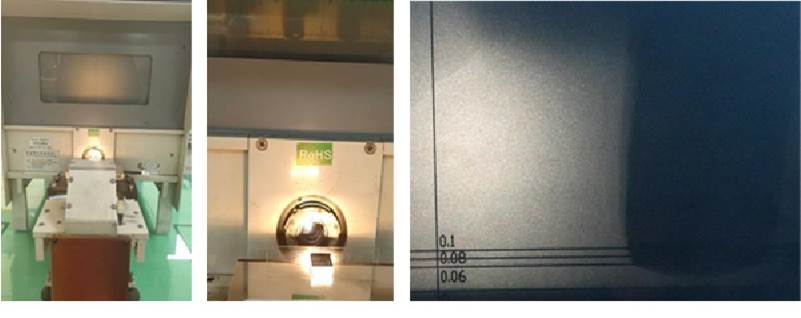
図3:0.08 mm以下のピンの足を投影しているところ
b. 実際に現場で作業状況を確認:投影時には製品を台の上に置きピンの足をを一つ一つ検査します。検査の基準線は3本ありますが、ピンの足が同時に3本の線を跨いでいます(図4のように)。この3本の線の間はわずかな距離しかないため、生産ラインの従業員は長時間作業からの視覚的な疲労で判断に誤差が現れ、それぞれのピンの足が0.1 mm以下の線にかかったものはうまく取り除くことができなかった時に不備が発生します。
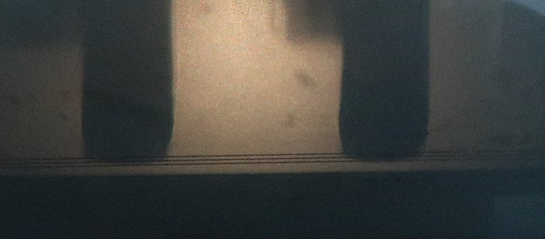
図4:ピンの足が同時に3本の線にかかる様子
- Step 2. FQC製品検査ステーション
製品の平坦度に対して抜き打ち検査を行いましたが平坦度は規格を超えたため検出できません。
- Step 3. 包装後のテープ検査ステーション
包装後の製品に対し外観について全て検査(図5のように)を行い、テープ内のピンの足が肉眼では検査を行いにくいためクライアント側に出荷してしまいました。
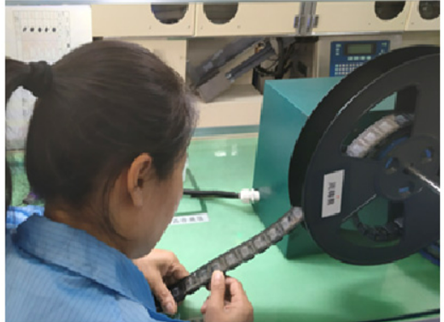
図5:外観検査
Solution:
1. 投影機の判定基準線を修正し、元の3本の線から1本(0.08 mm目盛のみを残す)に変更し誤審を防ぎます。
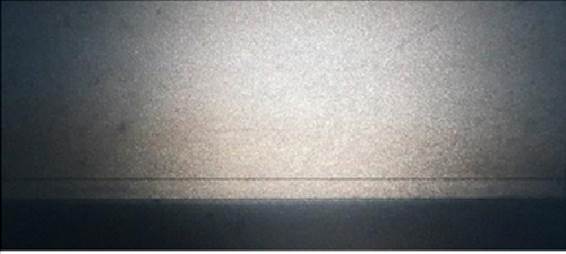
図6:0.08 mm目盛のみを残す
2. 投影機の基準線を修正したのち同機構製品を用いて検証を行い、2100 pcs製品を生産した上でFQC検査を行いました。もし不備がなければ生産後に生産品質状況及び納品状況を追うのを予定しています。フォローアップによるとこの新しいQC基準に合格した製品は、その後不備のRMAクレームは発生していません。
事例2. パーツのずれ
Spec:
モジュールのPAD/PINとPCBのPADは位置にずれが生じ、部品同士の幅は1/2を超えています。
不良率:3/726=4132DPPM
不良現象:
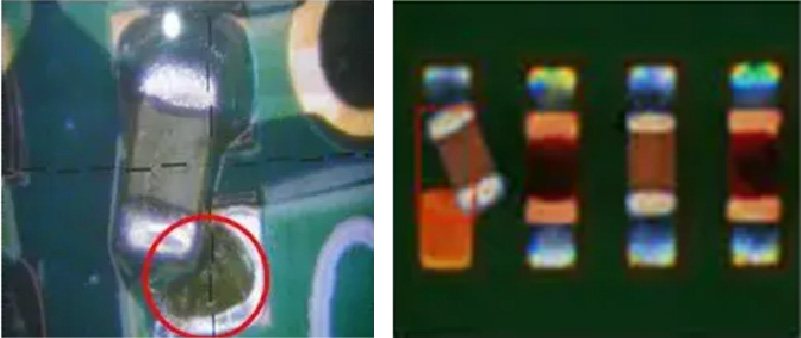
Root Cause:
1. ソルダーペーストは使用する際十分に時間に気を使わなければいけません。長い時間放置してしまいその中のフラックスが変質してしまうため溶接不良を引き起こししました。
2. ソルダーペースト自体の粘着力が弱く部品を運搬する時の揺れなどで部品がずれてしまいました。
3. ペースト中のフラックス含有量が高すぎたりリフローの溶接中にフラックスの流れ強すぎて部品がずれてしまいました。
4. 印刷やパッチ後の搬送中に部品が振動したり、正しく搬送されなかったりすることによる部品ずれになりました。
5. パッチ加工時、吸着ノズルの空気圧が調整しなかったため圧力が不足し部品がずれてしまいました。
6. パッチ自体の問題により、部品の設置位置が間違っています。
Solution:
1. 部品の取り付けの精度を上げるために位置決め時に座標を厳格に設定します。
2. 電子部品の表面実装の圧力を高め接着力を上げるために、品質が良く粘着力が強いソルダーペーストを使用します。
3. 適切なソルダーペーストを選びソルダーペーストの陥没を防止します。その時ソルダーペースト自体のフラックス含有量も適切です。
4. 貼付吸着ノズルの空気圧を調整し、部品の実装時は400 mmHG以上に設定します。
事例3. 錫の少ないパッド
Spec:
部品のピンの足とPCB、PADは錫溶接はあるが、錫の品質の基準に達していません。
不良率:2/425=4705 DPPM
不良現象:
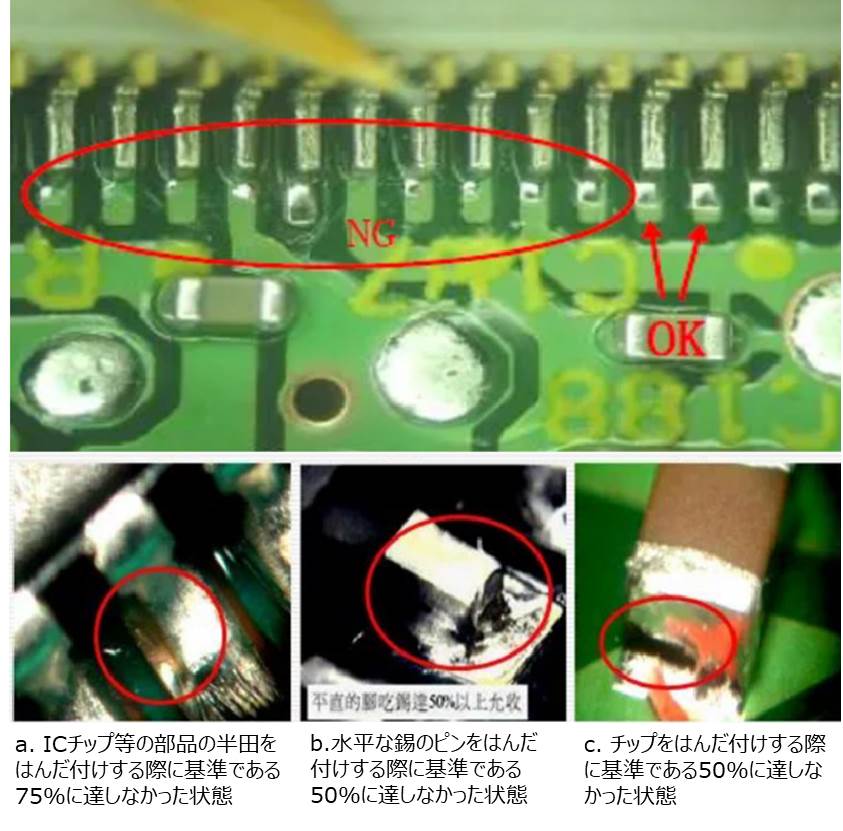
Root Cause:
1. 印刷停止時間が長く印刷スクリーン版開口部のフラックスが硬化してしまい塞がったしまいました
2. ソルダーペーストがうまく混ざったいないためパソコンのスクロールできなくなり、ソルダーペーストの劣化による粘度の増加と付着力の低下になります。
3. アリオン専門家チームの経験によると、ドクターブレードの不整合であることを推測します。
Solution:
1. SMTステンシルの清掃管理、または印刷開始時に一度印刷機を慣らします。ただフラックスが硬化してしまった場合は手動で洗浄する必要があります。
2. ソルダーペーストを開封するタイミングと使用時間を重点的に管理することや同様にソルダーペーストの攪拌管理を行います。
3. 電源を入れる前と定期的なドクターブレードの点検を行います。
事例4. メモリスロットショート
Spec:
不良率:3/726=4132DPPM
不良現象:
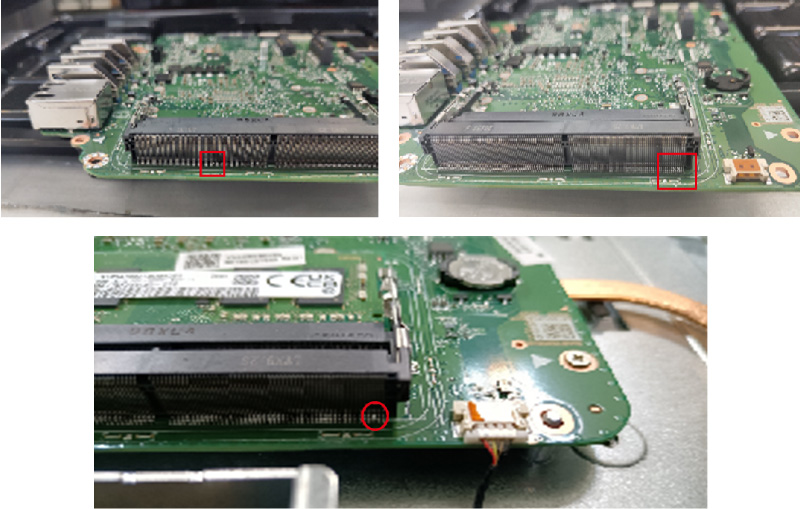
Root Cause:
1. 不良品実物を観察した結果、不備があったのは一方に集中するわけではないことが発見されました。このような不備はメモリスロット(RAM slot)のいかなる部位で発生する可能性があり、今回のショートはピン湾曲部位で発生していました。
2. リフロー溶接中に発生する可能性のあるショートを見つけるためにSPIレコードをトレースしました。
3. ソルダーペーストの生産記録を調べた結果、ソルダーペーストの使用量が前の機種より少し多いことが分かりました。
4. SMTステンシルのデータを調べたところSMTステンシルの開口部分は以前の機種に比べて大きいためパッド自体の錫の面積が多すぎる(1pcs当たり半田付けの面積が0.1 mm 2多い)ことが分かりました。
Solution:
1. SMTステンシルのパラメータの修正としてL*W =2mm*0.238 mm をL*W=1.85mm*0.22mm、パッドの半田付け面積を0.0619mm2 から 0.0529mm2へと変更します。
投影機の判定基準線を修正し、元の3本の線から1本(0.08 mm目盛のみを残す)に変更し誤審を防ぎます。
その内容は以下のとおりです:
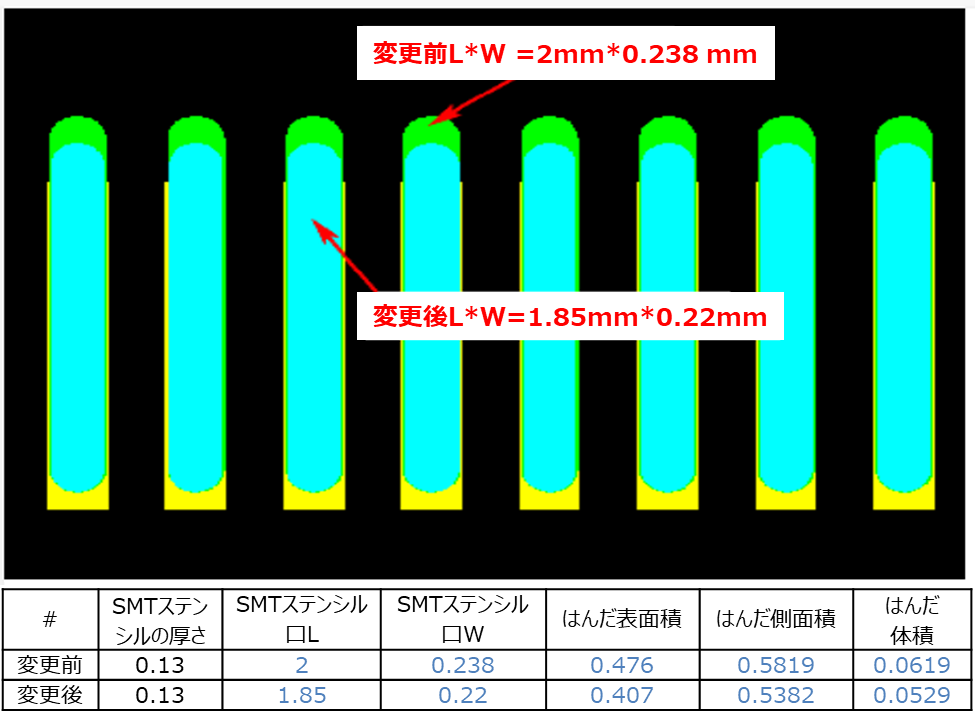
まとめ
以上の例から、たとえ工場自体にSMTのQC担当者がいたとしても第一段階では発見できない問題が多いことがわかります。これにより生産ラインの効率及び製品の品質の低下を危惧します。
アリオンの豊富なSMTQC検証サービスを通じて初期段階で圧倒的多数の問題を解決することができます。上記のSMTテストのほかにもアリオンはお客様の製品を応じたカスタマイズなテスト項目を実施することができます。IQC(入荷品質管理)からIPQC(プロセス管理)、製品出荷前のOQCまですべて提供しています。当社の品質管理プログラムにご興味をお持ちの方、またはご質問のある方は、お気軽にアリオンのお問い合わせフォームまでお問い合わせください。